Calling all electrical gurus, as this was never my strong subject.
I tried to make a wiring harness that would override the EKP when receiving a 12v signal from the hobbs switch. Essentially I wanted both pumps to receive 12v straight from the battery when boost was over 8 psi, with a diode on the EKP wiring that would supposedly protect it from back feeding.
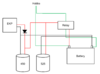
The diode is an NTE5991, rated for 40A 400V. Triple insulated with DEI heat sleeve since it got up to 150 degrees F. Datasheet is attached
After wiring everything, I jumped the hobbs switch with the car at idle. Instantly the fuel pressure went to 78 psi which is what I set the regulator at. I unhooked the test lead and shut off the car after running it like that for about 5 seconds. Put the car back together, attempted to start, no fuel pressure.
After figuring out the EKP was dead, I moved the trigger to fuse 8 (cigarette lighter) in the glove box and everything's been great.

Interesting thing is the car still "sees" the fuel pump, it just doesn't supply power to it. I left the diode even though it's probably not doing anything, and it doesn't get hot anymore. However there's no yellow "car on lift" service needed warning in the cluster, only a DME fault code:
CDA6 - Message (status, electric fuel pump, 0x335) faulty, receiver DME, transmitter EKP.
Usually the car gets unhappy when it no longer sees the fuel pump. When the EKP was working, if I unplugged the primary pump with the car running off the secondary, it would throw that yellow service needed warning in the cluster immediately.
Maybe someone who's better at DC circuits than me can explain exactly what happened here?
Side note, if Mike steps in here and tries to sell me his overpriced PWM controller I will tell everyone to boycott EOS.
I tried to make a wiring harness that would override the EKP when receiving a 12v signal from the hobbs switch. Essentially I wanted both pumps to receive 12v straight from the battery when boost was over 8 psi, with a diode on the EKP wiring that would supposedly protect it from back feeding.
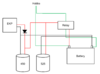
The diode is an NTE5991, rated for 40A 400V. Triple insulated with DEI heat sleeve since it got up to 150 degrees F. Datasheet is attached
After wiring everything, I jumped the hobbs switch with the car at idle. Instantly the fuel pressure went to 78 psi which is what I set the regulator at. I unhooked the test lead and shut off the car after running it like that for about 5 seconds. Put the car back together, attempted to start, no fuel pressure.
After figuring out the EKP was dead, I moved the trigger to fuse 8 (cigarette lighter) in the glove box and everything's been great.

Interesting thing is the car still "sees" the fuel pump, it just doesn't supply power to it. I left the diode even though it's probably not doing anything, and it doesn't get hot anymore. However there's no yellow "car on lift" service needed warning in the cluster, only a DME fault code:
CDA6 - Message (status, electric fuel pump, 0x335) faulty, receiver DME, transmitter EKP.
Usually the car gets unhappy when it no longer sees the fuel pump. When the EKP was working, if I unplugged the primary pump with the car running off the secondary, it would throw that yellow service needed warning in the cluster immediately.
Maybe someone who's better at DC circuits than me can explain exactly what happened here?
Side note, if Mike steps in here and tries to sell me his overpriced PWM controller I will tell everyone to boycott EOS.